Taking a Closer Look at Foam: Part 2 – Closed-Cell Foam
For the second part in our review of the cellular structure of our foam products, we take a look at the more rugged and durable closed-cell foams!
For the previous post in our two-part series, click here: Taking a Closer Look at Foam: Part 1 – Open-Cell Foam
—
Closed-Cell
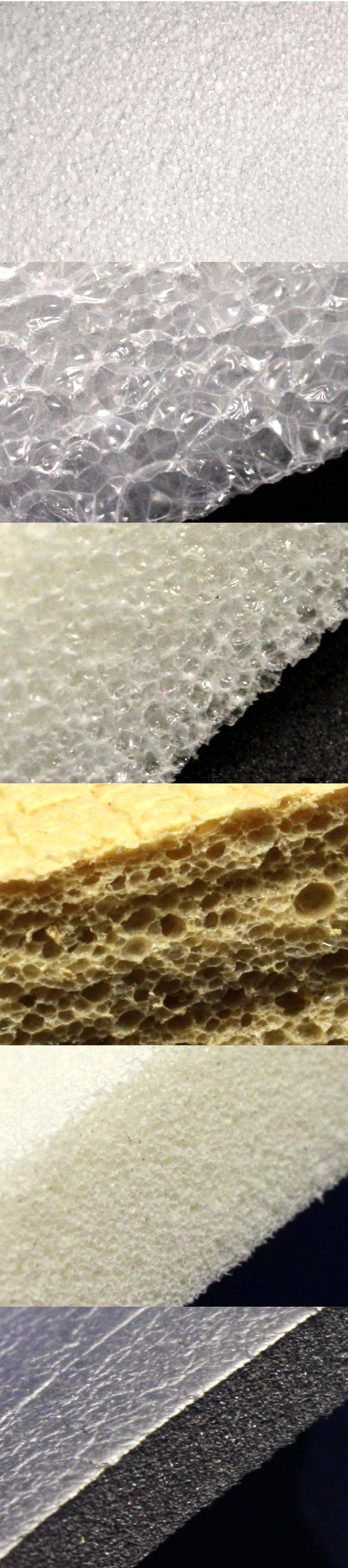
Top to Bottom: Polystyrene (EPS), Polyethylene, Polyethylene Roll, Gym Rubber, Cross-Linked Polyethylene (XLPE), Neoprene Click to Enlarge
While there is relatively little cellular variation among open-cell foams, closed-cell foam offers a range of cellular characteristics that can easily differentiate themselves from one another and are able to be seen with the naked eye.
Expanded Polystyrene (EPS) has the most unique foam cell structure among closed-cell foam, and as a result, is the most recognized. The ubiquitous white foam, typically seen as coffee cups and packaging materials, is also known as bead board because of its cellular structure. During the material’s formation, tiny beads of styrene expand to more than 40 times their original size and are compressed together into blocks, sheets, and molded shapes. These beads are easily seen in the structure of the material, and being about the size of a BB, can be picked out and held in your hand. Because of the size of these beads, EPS requires hotwire cutting for smooth edges, otherwise it tears and flakes.
Polyethylene is closed-cell foam that appears more plastic-like in appearance than its counterparts. Made in various colors, the material has a sheen, as opposed to the matte finish of some closed-cell foams that appear more rubbery. The cells of polyethylene are rather large, similar in size to Dryfast, but are completely sealed off to one another as enclosed cells. The size of the cells in polyethylene are impacted by the density of the material as well. Lower density polyethylene has larger cells and high density has smaller cells.
Very close structurally to standard polyethylene is polyethylene roll. Quite similar cellularly to standard polyethylene, the roll contains a much finer and consistent cellular structure but has some added sponge-like characteristics as well. Also unique is the skin on the top and bottom of sheets of polyethylene roll; not perfectly smooth as cells are still visible, but firmer than the foam’s interior.
Also similar to polyethylene is gym rubber, though its appearance can vary much more than the consistent polyethylene. As the name implies, gym rubber is more rubbery and less plastic-like than polyethylene, giving it a flatter-looking aesthetic. The cells in a gym rubber sheet are obscured by the smooth skin of the material, but a cross-section of the material shows a bubbly cellular setup. More than any other material The Foam Factory stocks, gym rubber can have the largest variation in cellular structure, ranging from minuscule to large cells.
The two foams with the finest cellular structures are the neoprene and cross-linked polyethylene (XLPE) varieties. The look and feel of these materials may make you think otherwise, but they are also constructed of cells, albeit incredible small ones. That cell size produces a material that looks more like a solid piece of flexible plastic or rubber than something built like the open-cell materials.
Both neoprene sheets and XLPE are consistent all the way through their forms, without getting denser near the outer edges of the sheet. Despite the visual similarities though, the compounds used to make these two materials produce different physical characteristics. The neoprene is the more rubbery material, softer in most formulations than XLPE, with more flexibility in most cases as well. Cross-linked polyethylene meanwhile, has more rigidity while usually being lighter. In thinner sheets, these two foam materials can be easily cut by hand with a sharp, non-serrated blade.
While there are many factors that affect a foam’s performance, having a little insight about a material’s structural makeup can give you a good starting point for deciding what might work well for you.
Tags: Gym Rubber, Neoprene, Polyethylene, Polystyrene, XLPE
Posted in Announcements
Leave a Reply